Active Vibration Isolation
Internal research
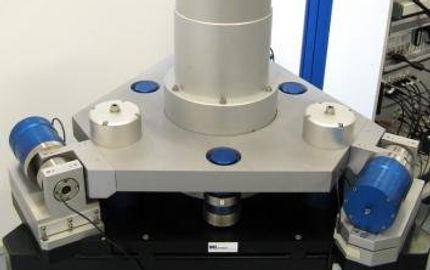
MI-Partners has developed a new active 6 degree-of-freedom vibration isolation platform.
Commercially available active vibration isolation systems basically are a combination of passive compliant suspension with active damping of the low frequent suspension modes. Broad application however has not yet occurred. Until now performance gain was limited and Horizontal-Tilt crosstalk asks for complex control strategies. Therefore the actual benefits appear not sufficient to accept the added cost. MI-partners has developed a new active vibration isolation platform with high performance, limited control complexity and high cost efficiency.
Fundamental improvements are made at two main aspects:
1) Elimination of Horizontal-Tilt crosstalk
Often geophone type of sensors are used in the active control (skyhook damping) as cost efficient solution. The drawback using these sensors lays in the fact that displacements caused by tilt of the payload are measured as horizontal displacements, introducing measurement errors and complex control actions to compensate. MI- partners introduces a patented sensor interface with which the crosstalk is eliminated and so omitting the need for control complexity.
2) Improved performance by noise reduction
Generally the vendors of isolation systems specify the performance of the system using the transfer function from floor vibrations to payload vibrations. To measure such curves, excitation of the floor or internal excitation with the actuators is used. Thus the signal levels are large enough to obtain clear curves showing large suppression of vibration at specific frequencies. For the actual system no external excitation is present and disturbance signals are generally very small. In such cases the noise from sensors and actuators becomes dominant. Using DEB (Dynamic Error Budgeting) methodology MI-partners specified all components of the active loop in the form of PSDs (Power Spectral Densities). Based on these specifications, improved sensor technology with extreme well small-signal-behavior is developed and integrated in a new high end vibration isolation platform.
​
​
Challenges
-
Reduce control complexity
-
Dynamic optimal sensor interface
-
Specification, development and realization of low noise components
Key Competences
-
Construction Principles for Precision Engineering
-
Dynamic Error Budgeting
-
Predictive Modeling
-
Motion Control
Results
-
Active performance below 50 μm/s2 vibration isolation platform on standard production floor
-
Patent pending sensor interface (no horizontal – tilt crosstalk)
-
Improved sensor/actuator technology
Cooperation
-
This project is sponsored by the European Regional Development Fund within the framework of Dutch OP-Zuid. Also sponsored by Het Rijk.
-
Magnetic Innovations with sensor and actuator technology
-
Mice BV
-
Two students from TU/e graduated at these subjects
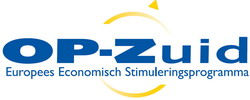

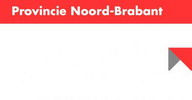